Din partner for måling, regulering og overvåking
Industriautomasjon - Klimateknologi - Hydraulikk - Motorer - Hydrogen - Testbenker - Jernbaner - Skipsbygging
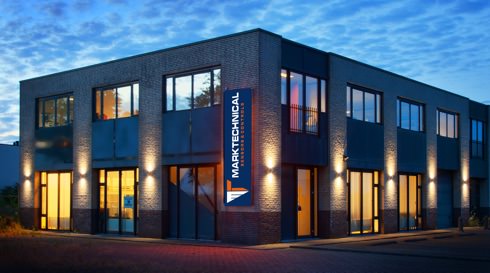
Marktechnical Sensorer og kontroller
Siden 1983 har Marktechnical levert måle- og kontrollinstrumenter for overvåking og kontroll av industrielle og maritime applikasjoner. For oss er kvalitet et konsept som handler om mye mer enn bare produktet. Alle våre prosesser er utformet med tanke på å kundeservice og produktkvalitet. Sortimentet omfatter: trykktransmittere, differensialtrykktransmittere, manometre, SF6-sensorer, termostater, temperatursensorer, dieseltermometre, strømningsmålere, strømningsbrytere, drivstofforbruksmålere, ultralydstrømningsmålere, fuktighetsmålere, digitale avlesninger, eksplosjonssikker instrumentering og lineær-rotatoriske servomotorer.
Certificaten en goedkeuringen voor de scheepsbouwindustrie
De hoogste kwaliteit is onze maatstaf!
Het productportfolio beschikt over de relevante goedkeuringen voor de scheepsbouwsector, zoals DNV-GL og IEC-Ex | ATEX-Ex voor temperatuur- en drukmeettechniek, alsmede Performance Level e og Functional Safety volgens SIL3 volgens EN 62061 / IEC 61508 en PL e volgens EN ISO 13849-1 voor krachtmeting.
Met onze meetoplossingen bent u altijd op koers!
Kategorier
Utvalgte produkter
Registratie voor Europort 2025 is geopend!
Met nog minder dan zes maanden te gaan, is het tijd om je klaar te maken voor hét maritieme evenement van het jaar! Europort 2025, de toonaangevende internationale maritieme vakbeurs, vindt plaats in Rotterdam Ahoy van 4 tot en met 7 november.
Stand: 1235, Hal 1
Schischek Heavy Duty Sensors & Actuators
Marktechnical distributiepartner van Hanbay
Hanbay levert geavanceerde elektrische aandrijvingen en actuatoren. Dankzij deze samenwerking kunnen wij met dit programma nog meer innovatieve en betrouwbare oplossingen bieden voor precieze ventielaandrijvingen voor uiteenlopende industriële toepassingen.
Følg med for de siste oppdateringene:
Maksimalt 1 nyhetsbrev per måned